
Pavement and Geotechnical Research
Pavement Research
The majority of transportation dollars are spent designing, constructing, and maintaining the nation's pavement system. Even the slightest improvement can have a tremendous impact on stretching taxpayer dollars and extending the longevity of the pavement. LTRC's pavement evaluation group investigates ways to improve roadway performance, extend the life of pavements, enhance safety, and reduce costs associated with construction, operation, and maintenance of the state highway system. This is accomplished through in-house and contract research programs.
LTRC technical capabilities include pavement evaluations for rideability, pavement distress analysis, pavement friction, non-destructive methods of pavement layer examinations, and pavement forensic analysis. The pavement group maintains a wide variety of specialized pavement evaluation equipment including the Falling Weight Deflectometer, Dynaflect, Pavement friction tester, and Automated profiler and Imaging system.
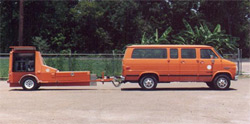
Dynaflect testing equipment
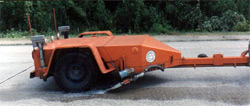
Pavement Research Facility
Rapid deterioration and premature failure of our nation's highway system are costly in time and money. In order to build more durable roads for tomorrow, it is imperative to find out today how pavements and materials will perform under repeated heavy loads. The Pavement Research Facility (PRF) provides an important bridge between laboratory characterization and long-term performance under heavy traffic loads.
The Pavement Research Facility, operated by LTRC, is staffed with an engineer manager, an electronics expert, and a mechanical expert. For each research project, research professors and engineers along with other LTRC staff augment the full time staff members. A technical advisory committee, comprised of members representing DOTD, FHWA, and state universities, provides direction and strategic planning for the research program. The facility is funded by the DOTD in cooperation with the Federal Highway Administration. Over $3 million has been invested in the site development, facility operation, and test bed construction at this state-of-art facility.
The PRF is strategically located on a six-acre site near LA 1 south, across the Mississippi River from Baton Rouge. With easy access to Interstate 10, Missouri Pacific Railroad, and the Intracoastal Waterway, materials can be conveniently transported to the site for accelerated loading studies. Pavement test sections are built with full-scale construction equipment closely simulating normal highway construction. The Accelerated Loading Facility (ALF) provides traffic loading.
ALFThe Accelerated Loading Facility device is a 100-ft long, 55-ton, accelerated loading device used to simulate truck loading for pavement testing. One of only three of its kind in the nation, ALF compresses many years of road wear into just a few months of testing. With a computer-controlled load trolley, the weight and movement of traffic is simulated repetitively in one direction with the load can be repeated every ten seconds around the clock. The load is adjustable from 10 thousands to 21 thousands pounds per ALF load application. By increasing the magnitude of load and running the device for 24 hours a day, it is possible to condense 20 years of loading into a period of only one month.
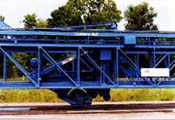
ALF testing device
Geotechnical Research
Karl Terzaghi, the "father of soil mechanics", once said; "Unfortunately, soils are made by nature and not by man, and the products of nature are always complex... As soon as we pass from steel and concrete to earth, the omnipotence of theory ceases to exist. Natural soil is never uniform. Its properties change from point to point while our knowledge of its properties are limited to those few spots at which the samples have been collected. In soil mechanics the accuracy of computed results never exceeds that of a crude estimate, and the principal function of theory consists in teaching us what and how to observe in the field." Therefore, geotechnical research is always playing an important role in providing less expensive solutions to the design and construction of transportation infrastructure.
LTRC geotechnical engineering research strives to bridge the gap between natural phenomenon, field experience and man's theory of these reactions to conduct implementable research that saves costs, time, and/or headaches through the use of new products or processes to improve the design, construction, and long-term performance of transportation infrastructure.
LTRC houses a fully equipped, modern soil laboratory capable of performing routine and advanced soils testing. Our Geotechnical laboratory equipment includes advanced testing apparatus such as stress path & triaxial strength testing, soil water characterization curve (SWCC), direct shear testing, consolidation testing and tensile/compression testing supported by an automated data acquisition system.
With recent advances in computers and electronics, our research program has expanded to include other researches like a Geotechnical Information Database, Continuous Compaction Control (intelligent compaction), and new Pile Vibration Monitoring Specifications. Our research will allow for quicker, more reliable and less labor intensive methods of design and/or in-situ testing, which can provide savings through better designed structures, embankments, and pavements.
Geotechnical Engineering Research Laboratory
What is GERL?
The Geotechnical Engineering Research Laboratory was established in 1989 to provide state-of-the-art research capabilities to assess the engineering properties of Geotechnical reinforced earth systems. Several research projects have been conducted to evaluate the influencing parameters affecting soil-Geotechnical interaction mechanism.
The LaboratoryThe laboratory hosts two large pullout boxes. Each box is 3 feet wide, 5 feet long and 2 feet high. The dimensions of the boxes permit testing representative specimen sizes of various types of metallic and geosynthetic reinforcements.
The hydraulic loading system in one of the boxes permits conducting long term pullout and confined extension tests on Geotechnical while the other box is being used for short term pullout tests. Direct shear tests to evaluate shear resistance at the Soil-Geotechnical interface are being conducted in a modified large direct shear box. The box has a shear area of 27 inches by 27 inches and uses the hydraulic loading system of one of the pullout boxes.
Tests are being conducted on reinforcements in both granular and cohesive soils. Results of the testing programs are incorporated in the design of reinforced soil walls, slopes and embankments.
Full-scale pullout tests were performed in the field on several mechanically stabilized earth walls. In-situ tests allowed developing methods for evaluating the testing parameters used in design through comparison with lab test results under similar testing conditions.
The GERL laboratory also hosts a system of five creep testing devices capable of applying constant hydraulic loads to evaluate the 10,000-hours creep characteristics of the geosynthetic specimens. Creep tests are also being conducted in temperature-controlled testing devices to evaluate the accelerated creep characteristics of Geotechnical. Accelerated tests permit evaluating creep characteristics of Geotechnical in short timed intervals.
GERL facility is housed in the LTRC research laboratories. In addition to these specialized facilities, LTRC also has standard testing equipment for evaluating the unconfined engineering properties of Geotechnical.